Workplace Safety Best Practices
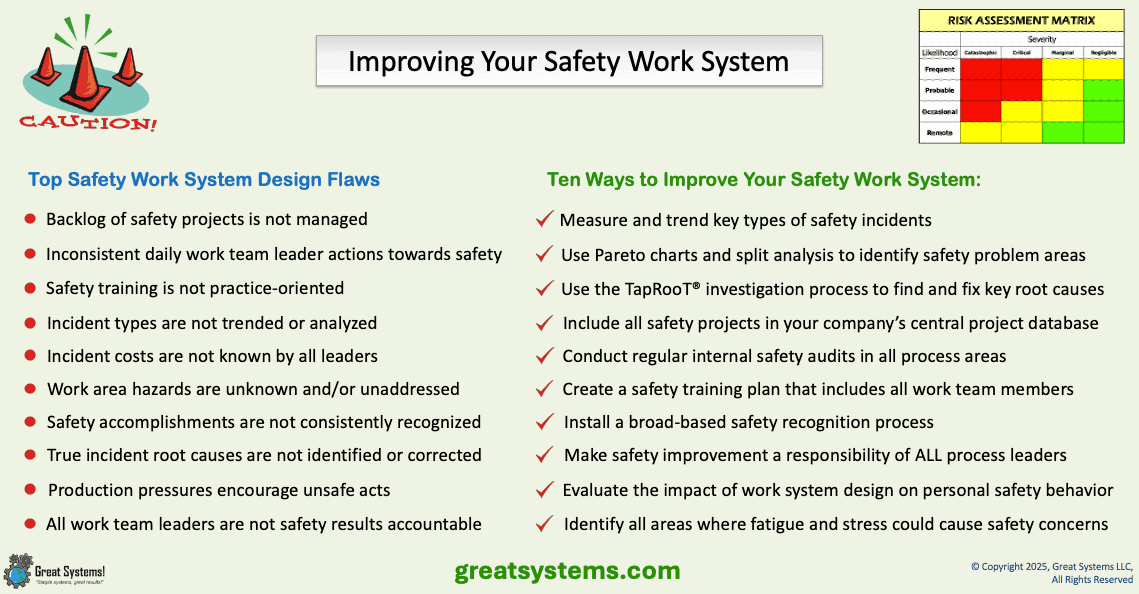
What Workplace Safety Best Practices Do You Use?
How many of the workplace safety best practices on this page do your work teams use to work injury-free daily?
In one of my current roles, I serve as a contract virtual TapRooT® root cause analysis and investigation process trainer, facilitator, and coach. This role gives me the chance each year to work with over 500 safety professionals from 30 or more organizations.
Over four decades, this level of exposure, coupled with my own personal experience in safety work system design and implementation, has taught me a lot.
For example, I now know what it takes to achieve and sustain very low incident rates. The work system changes one needs to make a shift from a reactive safety focus to a proactive safety focus are clear. I have found some great workplace safety best practices.
One of my biggest learnings over this time is simple, but not practiced by that many organizations. Each work team leader must demonstrate daily responsibility for the safety of their people.
As with process improvement, quality, or team development, you can't expect a department (such as the HSE or Engineering group) to keep your customers happy or your people safe. It must be a team effort. Safety is something that every leader is responsible, and held accountable for, every day.
In one of my current roles, I serve as a contract virtual TapRooT® root cause analysis and investigation process trainer, facilitator, and coach. This role gives me the chance each year to work with over 500 safety professionals from 30 or more organizations.
Over four decades, this level of exposure, coupled with my own personal experience in safety work system design and implementation, has taught me a lot.
For example, I now know what it takes to achieve and sustain very low incident rates. The work system changes one needs to make a shift from a reactive safety focus to a proactive safety focus are clear. I have found some great workplace safety best practices.
One of my biggest learnings over this time is simple, but not practiced by that many organizations. Each work team leader must demonstrate daily responsibility for the safety of their people.
As with process improvement, quality, or team development, you can't expect a department (such as the HSE or Engineering group) to keep your customers happy or your people safe. It must be a team effort. Safety is something that every leader is responsible, and held accountable for, every day.
Why Do Safety Performance Levels Vary Across Organizations and Locations?
As a virtual and onsite trainer for the TapRooT® investigation and root cause analysis process, I get the opportunity to meet and talk with safety professionals from around the world. These people represent companies that are at different places on the safety performance spectrum.
Some have gone months, if not years, without a lost time accident. They rarely have OSHA reportable incidents, even though other companies still experience fatalities.
As a performance improvement coach, there is one main question I continue to ask. Why is there such a difference in safety performance across these companies? You might think that the companies with the relatively weak safety records work in more hazardous environments. That is not always the case.
Some of our TapRooT® customers work in very hazardous work environments, such as offshore oil rigs or deep tunnel mines. Even so, their lost time and OSHA reportable rates are low, even in comparison to relatively safer industries.
Why does this performance difference exist? The answer is simple. These organizations use safety work system best practices.
Some have gone months, if not years, without a lost time accident. They rarely have OSHA reportable incidents, even though other companies still experience fatalities.
As a performance improvement coach, there is one main question I continue to ask. Why is there such a difference in safety performance across these companies? You might think that the companies with the relatively weak safety records work in more hazardous environments. That is not always the case.
Some of our TapRooT® customers work in very hazardous work environments, such as offshore oil rigs or deep tunnel mines. Even so, their lost time and OSHA reportable rates are low, even in comparison to relatively safer industries.
Why does this performance difference exist? The answer is simple. These organizations use safety work system best practices.
There is a measurable daily potential for human error that comes with any type of work people do. In order to optimize the use of necessary safe work practices, this error potential must be recognized by both the leaders and the team.
WATCH over 50 kaizen and workplace health improvement videos on my Great Systems YouTube channel.
WATCH over 50 kaizen and workplace health improvement videos on my Great Systems YouTube channel.
How Many Workplace Safety Best Practices Do You Use?
As a Plant Manager, Production Manager, Director of Quality, and Industrial Engineer, I know that a system gives you what you design it to give you. These companies have great safety records because they design their safety systems to produce better safety results. The companies that struggle to improve their safety records have relatively weak workplace safety systems and practices in place.
They may preach safety and have a safety professional on staff. People attend the required safety training each month. However, their safety work system lacks key design features.
Look at my "Top Ten" list of workplace safety system design flaws. Do any of the ten weaknesses sound familiar to you? If so, how many of them hold back your efforts to pursue safety process excellence?
Personally, I think personal safety is one of the easier performance areas to improve in. The other areas that I consider to be more of a challenge are cost, quality, and morale.
Do you struggle to attain better than average safety numbers? If so, you also probably have trouble with the quality of your products or services, the morale of your people, and your profit margins.
Why do I think safety is the easiest performance area to improve in? The answer is simple. You can more clearly see whether you have safety issues! Quality problems are typically more difficult to spot. Morale challenges are even more difficult to identify.
They may preach safety and have a safety professional on staff. People attend the required safety training each month. However, their safety work system lacks key design features.
Look at my "Top Ten" list of workplace safety system design flaws. Do any of the ten weaknesses sound familiar to you? If so, how many of them hold back your efforts to pursue safety process excellence?
Personally, I think personal safety is one of the easier performance areas to improve in. The other areas that I consider to be more of a challenge are cost, quality, and morale.
Do you struggle to attain better than average safety numbers? If so, you also probably have trouble with the quality of your products or services, the morale of your people, and your profit margins.
Why do I think safety is the easiest performance area to improve in? The answer is simple. You can more clearly see whether you have safety issues! Quality problems are typically more difficult to spot. Morale challenges are even more difficult to identify.
What Do You Focus On More – Unsafe Conditions or Unsafe Acts?
When I say this, you might think that I mean you can see work area hazards, so you ought to be able to eliminate them. While this is true, I am speaking much more about unsafe acts than I am about unsafe conditions.
Most safety professionals know that most accidents are a result of unsafe acts, versus unsafe conditions. The great thing about safety is that we can also see unsafe acts, just as easily as we can see unsafe conditions.
The problem is that we don’t have systematic approaches in place to (1) regularly identify unsafe acts and (2) consistently address these unsafe acts when we see them IN AN EFFECTIVE MANNER. A sound near-miss program or behavior-based safety program should do this. Unfortunately, far too few organizations have such approaches in place.
When they do, these approaches are often poorly designed and even more poorly executed. However, the problems are still easy to spot.
Most safety professionals know that most accidents are a result of unsafe acts, versus unsafe conditions. The great thing about safety is that we can also see unsafe acts, just as easily as we can see unsafe conditions.
The problem is that we don’t have systematic approaches in place to (1) regularly identify unsafe acts and (2) consistently address these unsafe acts when we see them IN AN EFFECTIVE MANNER. A sound near-miss program or behavior-based safety program should do this. Unfortunately, far too few organizations have such approaches in place.
When they do, these approaches are often poorly designed and even more poorly executed. However, the problems are still easy to spot.
Who Should Use Workplace Safety Best Practices to Improve Performance?
This is the biggest challenge that faces those companies who struggle to improve their safety records. In these companies, safety improvement is seen as the responsibility of the safety professional, the safety department, or someone else other than the work team leader (the process owner).
In these organizations, EACH work team leader (manager, supervisor, or lead person) IS NOT required to identify and correct the safety concerns that exist in their area on a consistent basis. Such work is left up to the safety professional.
Work team leaders might have safety measures in their performance expectations. Unfortunately, we rarely expect these people to demonstrate HOW they change their work systems to make the numbers improve.
They count on the safety people or the engineers (or threats and fear tactics) to make them look good at the annual review. This is not a sustainable, or recommended, approach.
The need for safety improvement may show up as a sentence or two in a work team leader job description, but how do they approach their jobs each day? Look at how they spend their time. Listen to the types of things they say when they talk with their people.
How much of a safety focus do you see? Such behavior is a cultural problem. However, it is also the leverage point where significant safety gains can be made.
In these organizations, EACH work team leader (manager, supervisor, or lead person) IS NOT required to identify and correct the safety concerns that exist in their area on a consistent basis. Such work is left up to the safety professional.
Work team leaders might have safety measures in their performance expectations. Unfortunately, we rarely expect these people to demonstrate HOW they change their work systems to make the numbers improve.
They count on the safety people or the engineers (or threats and fear tactics) to make them look good at the annual review. This is not a sustainable, or recommended, approach.
The need for safety improvement may show up as a sentence or two in a work team leader job description, but how do they approach their jobs each day? Look at how they spend their time. Listen to the types of things they say when they talk with their people.
How much of a safety focus do you see? Such behavior is a cultural problem. However, it is also the leverage point where significant safety gains can be made.
What Components Make Up a Well-Designed Safety Work System?
The “Safety System Star” contains five key components - measures, recognition, procedures, improvement processes, and workgroup meetings. These five components should be part of any well-rounded safety system.
Some safety systems contain additional components. If you can find a way to at least build the approaches that are shown here into your safety system over time, you will find that it will produce better, and more sustainable, results.
My experience shows me that of the four areas, companies tend to be the weakest in the ‘Measures’, ‘Recognition’, and ‘Improvement Processes’ areas. In such cases, meetings and training regularly occur. However, these practices are often much less effective than they could be.
Don’t just take my word for it though. Review the safety star yourself. Where do you currently have approaches in place that work well and where you don’t? How effectively do you use safety system best practices?
Some safety systems contain additional components. If you can find a way to at least build the approaches that are shown here into your safety system over time, you will find that it will produce better, and more sustainable, results.
My experience shows me that of the four areas, companies tend to be the weakest in the ‘Measures’, ‘Recognition’, and ‘Improvement Processes’ areas. In such cases, meetings and training regularly occur. However, these practices are often much less effective than they could be.
Don’t just take my word for it though. Review the safety star yourself. Where do you currently have approaches in place that work well and where you don’t? How effectively do you use safety system best practices?
Work team leaders drive the use of workplace safety best practices
Do you want real safety improvement to happen in a fast and sustainable manner? If so, you must do three things.
First, you must change the job descriptions of each work team leader to include specific safety responsibilities.
Second, use both lagging (incident rates) and leading (high risk behavior rates) indicators to monitor safety performance.
Third, require each owner to PROVE HOW they consistently change their work systems to help obtain better safety results. Don't tolerate poor performance. If a work team leader fails to meet job expectations, provide a coach and support for at least year.
Then, expect quarterly improvement over that year. If your leaders fail to consistently practice the changes that you desire, help them find a different role to fill.
First, you must change the job descriptions of each work team leader to include specific safety responsibilities.
Second, use both lagging (incident rates) and leading (high risk behavior rates) indicators to monitor safety performance.
Third, require each owner to PROVE HOW they consistently change their work systems to help obtain better safety results. Don't tolerate poor performance. If a work team leader fails to meet job expectations, provide a coach and support for at least year.
Then, expect quarterly improvement over that year. If your leaders fail to consistently practice the changes that you desire, help them find a different role to fill.
Reactive Investigations Help Identify Workplace Safety System Gaps
Why do you invest time in incident investigations? Are your efforts merely to meet legal requirements, or do you expect work system design change as well?
Too many people expect the incident's elimination as a goal. Unfortunately, they don't also see reactive analysis as a chance to eliminate poor work system designs for good.
Too many people expect the incident's elimination as a goal. Unfortunately, they don't also see reactive analysis as a chance to eliminate poor work system designs for good.
Personal Safety Work System Analysis and Design
I can work with your safety committee or management team to design and execute a comprehensive plan to improve workplace safety. Plus, I can help you minimize the potential for on-the-job injuries.
Typical system components include a monthly internal audit process, safety committee setup, an investigation process for near misses and reportable injuries, safety training curriculum and material design, a project management process, and monthly safety reporting tools.
Additionally, I can help you set up a behavior-based safety system and a scorecard of leading safety indicators. In each case, these workplace safety best practices will help you address potential safety problems before they become real ones.
Typical system components include a monthly internal audit process, safety committee setup, an investigation process for near misses and reportable injuries, safety training curriculum and material design, a project management process, and monthly safety reporting tools.
Additionally, I can help you set up a behavior-based safety system and a scorecard of leading safety indicators. In each case, these workplace safety best practices will help you address potential safety problems before they become real ones.
TapRooT® Root Cause Analysis and Investigation Training
I have taught over 450 courses and helped more than 600 organizations as a certified virtual contract trainer for the TapRooT® root cause analysis process. I believe that this approach to root cause analysis far exceeds the more opinion-based approaches that have been in use for years.
Such approaches include fishbone diagrams, 5 Whys, and fault tree analysis. Additionally, the TapRooT® root cause tree represents a collection of 103 best practices for reducing human error and performance challenges.
In turn, you can use the process to error proof your work systems. Do you want to reduce the potential for accidents, minimize significant amounts of waste, improve customer satisfaction levels, and grow your business? If so, you need work systems that promote effective, daily human performance and minimize the potential for equipment breakdowns.
Such approaches include fishbone diagrams, 5 Whys, and fault tree analysis. Additionally, the TapRooT® root cause tree represents a collection of 103 best practices for reducing human error and performance challenges.
In turn, you can use the process to error proof your work systems. Do you want to reduce the potential for accidents, minimize significant amounts of waste, improve customer satisfaction levels, and grow your business? If so, you need work systems that promote effective, daily human performance and minimize the potential for equipment breakdowns.
Incident Investigation Facilitation and Safety Work System Redesign
Some of my TapRooT® customers can't seem to make go away on their own. That's when they enlist my services. I can help you find the systemic causes of such problems.
To do this, I use of a combination of virtual investigation interviews and facilitation, work systems analysis, workplace observation, and virtual coaching. I will help you easily install workplace safety best practices you need to minimize injury risk.
>More importantly, I can help you identify effective corrective actions, (systems changes) that can be put in place to help minimize the likelihood that these problems will come back in the future. I can also help you improve your existing investigation process so that it routinely produces better results in less time.
If you would like to learn more about the safety work system best practices and improvement tools I have to offer, please send me an e-mail at kevin@greatsystems.com!
To do this, I use of a combination of virtual investigation interviews and facilitation, work systems analysis, workplace observation, and virtual coaching. I will help you easily install workplace safety best practices you need to minimize injury risk.
>More importantly, I can help you identify effective corrective actions, (systems changes) that can be put in place to help minimize the likelihood that these problems will come back in the future. I can also help you improve your existing investigation process so that it routinely produces better results in less time.
If you would like to learn more about the safety work system best practices and improvement tools I have to offer, please send me an e-mail at kevin@greatsystems.com!