Top Seven Equipment Reliability Improvement Tips
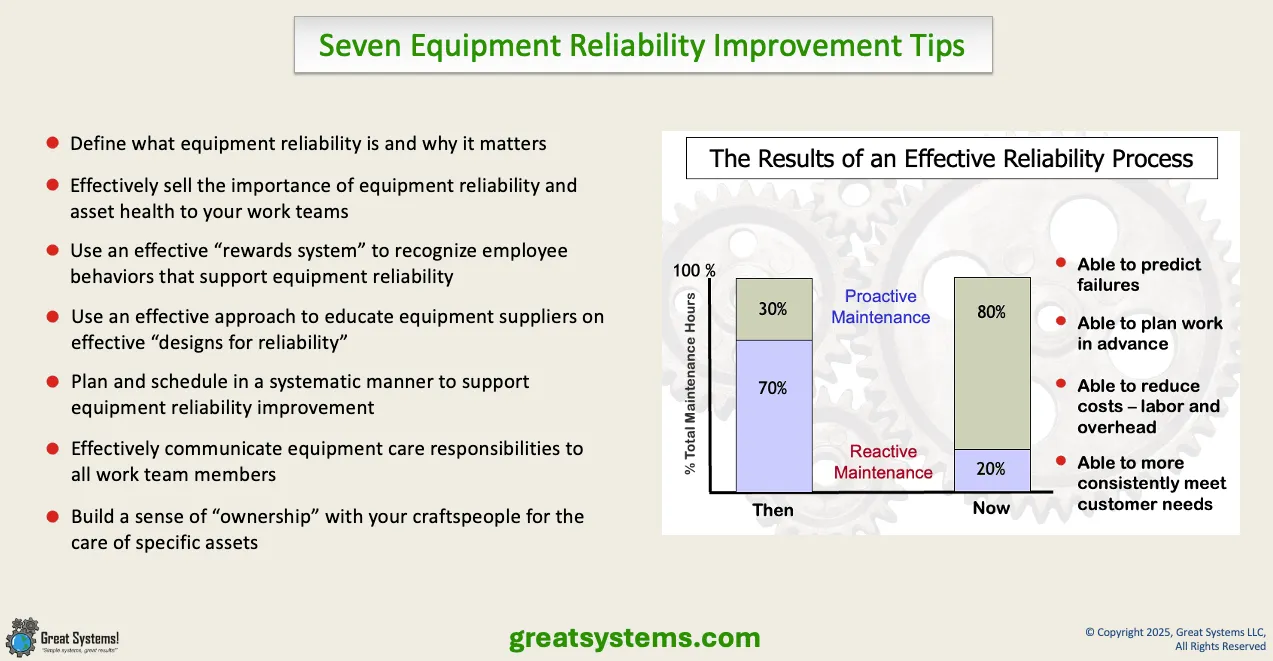
My Top Seven Equipment Reliability Improvement Tips
How can my top seven equipment reliability improvement tips help your work teams save time and money, reduce failures, and optimize output? My hope is that you use them to help create an effective equipment reliability improvement process. Such a process provides an organization with two key benefits.
First, an effective equipment reliability process helps minimize operational costs. More importantly, it helps ensure that the company can deliver the products or services its customers desire. Equipment reliability may be a hot topic. However, too many organizations continue to struggle to put a formal equipment reliability system in place.
Here are my top seven equipment reliability improvement tips I have learned from my applications in multiple organizations.
Be a part of my 2-day ‘Measurement, Trending, and Predictive Analytics – How the Best Use Data to Improve’ workshop on September 29-30. It’s part of the 2025 TapRooT® Summit in Knoxville, TN.
First, an effective equipment reliability process helps minimize operational costs. More importantly, it helps ensure that the company can deliver the products or services its customers desire. Equipment reliability may be a hot topic. However, too many organizations continue to struggle to put a formal equipment reliability system in place.
Here are my top seven equipment reliability improvement tips I have learned from my applications in multiple organizations.
Be a part of my 2-day ‘Measurement, Trending, and Predictive Analytics – How the Best Use Data to Improve’ workshop on September 29-30. It’s part of the 2025 TapRooT® Summit in Knoxville, TN.
Tip #1: Define what equipment reliability means and why it is important
What does equipment reliability mean in your organization? Why is it important?
>To many, it is no more than an equipment downtime reduction effort. However, equipment reliability improvement involves more than that.
True, there are the twin goals of (1) downtime frequency and (2) downtime duration reduction. Improvements in both areas lead to an increase in the mean time between failure (MTBF). Such gains help reduce process costs. Plus, these gains improve product / service quality.
Also, an effective equipment reliability process includes a focus on process output optimization while the process (equipment) is online. However, all three goals are lagging indicators that improve as asset health improves.
You can use indexes and trends to measure asset health across multiple performance areas, such pressure, speed, and temperature. Asset health indexes improve as a result of effective indicator monitoring, coupled with the implementation of improvement projects that address high risk failure areas.
>To many, it is no more than an equipment downtime reduction effort. However, equipment reliability improvement involves more than that.
True, there are the twin goals of (1) downtime frequency and (2) downtime duration reduction. Improvements in both areas lead to an increase in the mean time between failure (MTBF). Such gains help reduce process costs. Plus, these gains improve product / service quality.
Also, an effective equipment reliability process includes a focus on process output optimization while the process (equipment) is online. However, all three goals are lagging indicators that improve as asset health improves.
You can use indexes and trends to measure asset health across multiple performance areas, such pressure, speed, and temperature. Asset health indexes improve as a result of effective indicator monitoring, coupled with the implementation of improvement projects that address high risk failure areas.
Effective measures play a key role in the proactive assessment of asset health. Such measures extend well beyond the traditional measurement of asset uptime or downtime. What work process vital do you monitor and trend to measure asset health and failure potential?
WATCH over 50 kaizen and workplace health improvement videos on my Great Systems YouTube channel.
WATCH over 50 kaizen and workplace health improvement videos on my Great Systems YouTube channel.
Tip #2: Effectively sell the importance of equipment reliability and asset care to your work team
Most people do not like to live with the headaches they experience on the job each day. Your work team may gain a sense of self satisfaction when they put out equipment failure 'fires.' However, they gain a much higher level of pride when they put these fires out for good. Use success stories to show your work teams how equipment reliability gains help take away their downtime headaches. If you can, you are in a better position to sell them on the need for an equipment reliability and asset care focus.
Involve work team members in your equipment reliability improvement efforts. Avoid the temptation to let some other group in the company come in and ‘do it for them.’ Let work team members know ahead of time how their daily job will change if they are successful. To what degree will they need to 'do more with less?' How will their daily tasks change? How will they use their work time differently if downtime is minimized, and throughout is optimized, to a significant degree?
Involve work team members in your equipment reliability improvement efforts. Avoid the temptation to let some other group in the company come in and ‘do it for them.’ Let work team members know ahead of time how their daily job will change if they are successful. To what degree will they need to 'do more with less?' How will their daily tasks change? How will they use their work time differently if downtime is minimized, and throughout is optimized, to a significant degree?
Tip #3: Use an effective “rewards system” to recognize employee behaviors that support equipment reliability
The least effective (and most damaging) form of rewards is the 'one winner' system. Avoid the use of any recognition system such as ‘employee of the month’ that recognizes only one person at the expense of others. Instead, put in place a reward system that recognizes anyone who meets, or exceeds, certain criteria. Secondly, don't reward someone for ‘simply’ doing their daily job.
The best form of reward system for any improvement effort is a well-designed profit share plan. Such plans allow employees at all levels to obtain some additional amount of pay when site or organizational goals are met. The most effective plans have a short line of sight (monthly payouts for example), are based on achieving a balanced set of performance goals, and vary in amount as a greater percentage of the desired goal set is achieved.
Within such a system, equipment reliability improvements would be evident in downtime reductions, process output increases, and lower equipment replacement needs. Plus, such improvements result in lower operating costs.
Other forms of formal recognition include gift certificates or free meals for work team members that help implement an improvement which significantly impacts reliability. Many organizations are hesitant to pursue a full blown profit share approach. Instead, they pursue such a less complex route. For starters, define (1) formal recognition budget amounts, (2) what types of contributions to recognize, and (3) who will be eligible for such recognition.
Most importantly, realize that in a work system, individuals (such as an engineer) are rarely successful on their own. In turn, it sends a negative message to other team members if that individual is recognized and they are not, or if that individual is recognized to an inequitable degree.
The best form of reward system for any improvement effort is a well-designed profit share plan. Such plans allow employees at all levels to obtain some additional amount of pay when site or organizational goals are met. The most effective plans have a short line of sight (monthly payouts for example), are based on achieving a balanced set of performance goals, and vary in amount as a greater percentage of the desired goal set is achieved.
Within such a system, equipment reliability improvements would be evident in downtime reductions, process output increases, and lower equipment replacement needs. Plus, such improvements result in lower operating costs.
Other forms of formal recognition include gift certificates or free meals for work team members that help implement an improvement which significantly impacts reliability. Many organizations are hesitant to pursue a full blown profit share approach. Instead, they pursue such a less complex route. For starters, define (1) formal recognition budget amounts, (2) what types of contributions to recognize, and (3) who will be eligible for such recognition.
Most importantly, realize that in a work system, individuals (such as an engineer) are rarely successful on their own. In turn, it sends a negative message to other team members if that individual is recognized and they are not, or if that individual is recognized to an inequitable degree.
Tip #4: Use an effective approach to educate equipment suppliers on effective “designs for reliability”
One of the best approaches to use is the regular supplier conference, which the organization hosts on at least an annual basis. Some key suppliers may require quarterly meetings of this nature. This is especially true in the first year or so of the transition to an equipment reliability focus.
During these meetings, reviews of company expectations, current trends, and best practices occur. Plus, leaders can include key suppliers on concurrent engineering design teams as a second method to educate and engage them. Finally, well-defined equipment specifications help suppliers provide the degree of equipment performance that is expected.
Keep in mind how the supplier agreement for a given job, along with the supplier management system, affects supplier knowledge and performance. Both processes play foundational roles that help ensure suppliers keep their skills relative to reliability design up-to-date.
Also, these processes help suppliers incorporate these design factors into the products and services they provide to the organization. Too many organizations simply negotiate with a supplier on price. They fail to consider the often more important factors of design soundness, design for reliability, and user friendliness as part of the agreement and supplier evaluation system.
During these meetings, reviews of company expectations, current trends, and best practices occur. Plus, leaders can include key suppliers on concurrent engineering design teams as a second method to educate and engage them. Finally, well-defined equipment specifications help suppliers provide the degree of equipment performance that is expected.
Keep in mind how the supplier agreement for a given job, along with the supplier management system, affects supplier knowledge and performance. Both processes play foundational roles that help ensure suppliers keep their skills relative to reliability design up-to-date.
Also, these processes help suppliers incorporate these design factors into the products and services they provide to the organization. Too many organizations simply negotiate with a supplier on price. They fail to consider the often more important factors of design soundness, design for reliability, and user friendliness as part of the agreement and supplier evaluation system.
Tip #5: Plan and schedule in a systematic manner to support equipment reliability improvement
To improve equipment reliability, employ plan and schedule work in a systematic manner. Without a formal process, it is difficult to ensure that leaders effectively allocate time and money resources to those areas that most need them.
Instead, one or two high visibility projects receive all of the focus at the expense of other projects that actually may provide more value.
Many efforts to improve reliability fail simply because the ‘squeaky wheel’ gets the grease, instead of other areas that are actually more critical to performance improvement. Unfortunately, leaders often discount preventive maintenance activities, even when a formal reliability process is in place.
Often, this occurs when a reactive work culture exists in an organization. For success, develop sound cost / benefit analyses for each potential improvement option. For example, evaluate how throughput improvement can lead to sales volume increases.
Instead, one or two high visibility projects receive all of the focus at the expense of other projects that actually may provide more value.
Many efforts to improve reliability fail simply because the ‘squeaky wheel’ gets the grease, instead of other areas that are actually more critical to performance improvement. Unfortunately, leaders often discount preventive maintenance activities, even when a formal reliability process is in place.
Often, this occurs when a reactive work culture exists in an organization. For success, develop sound cost / benefit analyses for each potential improvement option. For example, evaluate how throughput improvement can lead to sales volume increases.
Tip #6: Effectively communicate equipment care responsibilities to all work team members
The most common approaches to communicate job responsibilities of any nature are the job description, the compensation system, the personal development process, and the measurement system. First, the job description defines what needs to be done each day. Plus, it clarifies how much time to spend on key types of work and how to measure that work. Second, the compensation work system rewards people who do work that is consistent with expectations.
An effective personal development process serves as the primary vehicle to address performance that fails to meet expectations. Finally, the measurement work system helps communicate expectations. Its mix of measures sends a strong message about relative task importance.
Also, work team leaders play a key role in communicating performance expectations, including those of a reliability nature. These people choose what to cover in formal meetings. Plus, they determine how much emotion and time to devote to each agenda item. Supervisors and managers make daily decisions about what performance issues they choose to recognize positively, provide negative feedback on, or ignore. In each case, they send messages to work team members about what is important, and what is not.
Most organizations employ all of these approaches to some degree. The challenge is use them effectively. Accept the fact that effectiveness is tough to determine without some form of measurement for each approach. Your process measurement process helps (1) identify design gaps you can close via process refinements and (2) the relative impact of such refinements.
An effective personal development process serves as the primary vehicle to address performance that fails to meet expectations. Finally, the measurement work system helps communicate expectations. Its mix of measures sends a strong message about relative task importance.
Also, work team leaders play a key role in communicating performance expectations, including those of a reliability nature. These people choose what to cover in formal meetings. Plus, they determine how much emotion and time to devote to each agenda item. Supervisors and managers make daily decisions about what performance issues they choose to recognize positively, provide negative feedback on, or ignore. In each case, they send messages to work team members about what is important, and what is not.
Most organizations employ all of these approaches to some degree. The challenge is use them effectively. Accept the fact that effectiveness is tough to determine without some form of measurement for each approach. Your process measurement process helps (1) identify design gaps you can close via process refinements and (2) the relative impact of such refinements.
Tip #7: Build a sense of “ownership” with your craftspeople for the care of specific assets
To establish ownership, you must (1) define the expectation of process ownership and (2) empower people to take initiative to make improvements to those processes. To increase ownership levels, give your maintenance work teams key process feedback on a regular basis.
Provide the time and money resources to help them succeed. It is management's role to make the requisite work system changes to help minimize human error and equipment problems outside the control of these people. Finally, consistently recognize craftspeople, both informally and formally, when they demonstrate a sense of ownership through measurable results.
Provide the time and money resources to help them succeed. It is management's role to make the requisite work system changes to help minimize human error and equipment problems outside the control of these people. Finally, consistently recognize craftspeople, both informally and formally, when they demonstrate a sense of ownership through measurable results.
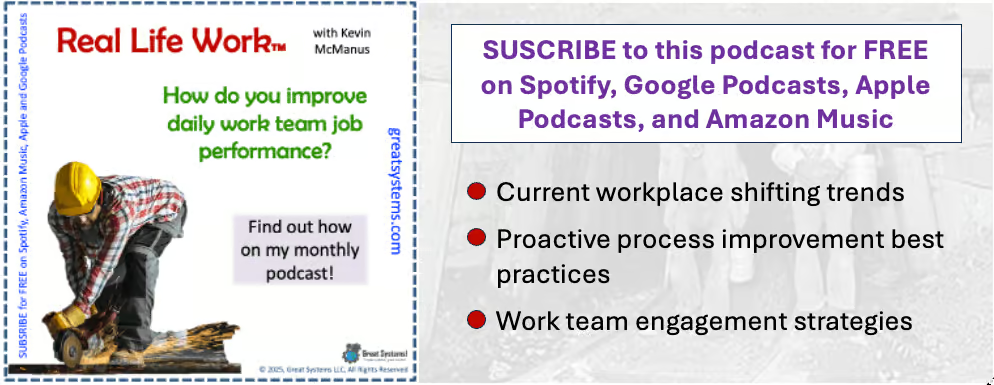
LISTEN NOW to my 'Seven Equipment Reliability Improvement tips' Real Life Work podcast.
Key Reliability Work Culture Questions to Consider
Assess your own belief systems as a leadership team. Do you believe that people come to work with the desire to do a good job? Do you think people will cut corners any chance they get? How often do you blame people when problems arise? Is it your tendency to search for those systemic factors that by design could encourage higher levels of human error?
Do you believe that equipment failures are simply a fact of life? Does your management team attempt to identify and remedy those systemically induced human errors that lead to a higher frequency and severity of equipment problems? People are much more reluctant to take ownership if they perceive they are left out on an island. Does management help them succeed or set them up for failure?
Do you believe that equipment failures are simply a fact of life? Does your management team attempt to identify and remedy those systemically induced human errors that lead to a higher frequency and severity of equipment problems? People are much more reluctant to take ownership if they perceive they are left out on an island. Does management help them succeed or set them up for failure?