Best Practice Work System Downloads
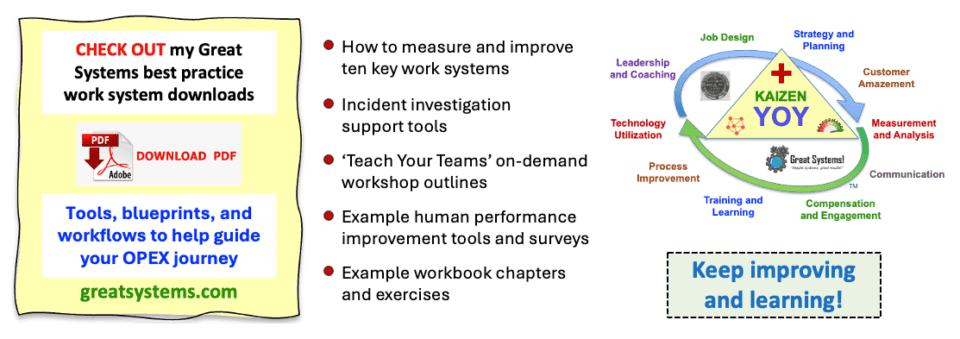
20+ Best Practice Work System Downloads!
Here you will find a variety of best practice work system downloads that you can use right away. The free downloads are examples of content from my work experiences and workbook creation efforts.
I plan to continue to add content to this page over the coming months, so please plan a return visit. Please message me if there is some other form of continuous improvement support content that I might be available to provide here.
I plan to continue to add content to this page over the coming months, so please plan a return visit. Please message me if there is some other form of continuous improvement support content that I might be available to provide here.
Root Cause Analysis Investigation Support
I give out these handouts when I teach a 3-day TapRooT® Virtual Root Cause Analysis course. Their goal is to help you ask better root cause analysis questions and streamline your investigation process.
DOWNLOAD my 2025 Incident Investigation Support Handouts
DOWNLOAD my 2025 Example Incident Investigator Position Observation Checklist PDF
DOWNLOAD my 'Five Bad Root Cause Analysis Questions and 24 Great Ones' PDF
DOWNLOAD my 'How to Measure Investigator Competency' PDF
DOWNLOAD my 'How to Measure and Evaluate Workplace Safeguard Effectiveness' PDF
DOWNLOAD my 2025 Incident Investigation Support Handouts
DOWNLOAD my 2025 Example Incident Investigator Position Observation Checklist PDF
DOWNLOAD my 'Five Bad Root Cause Analysis Questions and 24 Great Ones' PDF
DOWNLOAD my 'How to Measure Investigator Competency' PDF
DOWNLOAD my 'How to Measure and Evaluate Workplace Safeguard Effectiveness' PDF
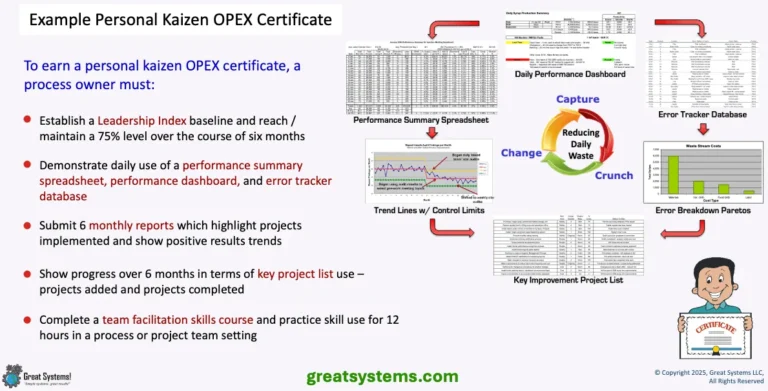
Great Systems Personal Kaizen Operational Excellence Certificate Process
This download details the steps that make up my Personal Kaizen Operational Excellence Certificate process. This process has helped front line leaders in a variety of work settings improve their effectiveness as NextGen workplace leaders.
My 'Best Practice Work System' downloads are designed to give you ways to change your work systems and produce better results. I hope that you take the time to explore the variety of tools and ideas I share on this site. Keep improving!
'How to Change Work Culture' Book Sample
This download gives you a sample chapter from my 'How to Develop a High-Performance Work Culture' book. I first wrote this book in 2006. Unfortunately, too many organizations have yet to even install the basic work systems I share in this book.
My 168-page, full color 'How to Change Work Culture' workbook and its exercises helps you and your team learn you learn how work systems shape work cultures. Their use helps blend team and organizational work cultures into one consistent, culture where kaizen is a daily work habit. Plus, I have 'personal use' experience with all of the tools I share from my past workplaces that I am happy to share.
DOWNLOAD my High Performance Work Culture Book Sample PDF
Do you want to 'stop the insanity' and eliminate the need to chase fads? If so, this workbook is for you. It contains strategies and complete exercises that give you better culture shift results in less time, and at a lower cost. Plus, you can customize my virtual or live 'How to Change Work Culture' workshop to meet the needs of any workplace.
*FREE* 'How to Change Work Culture' workbooks!
With my current update of this now-vintage, but still very value added, workbook comes the creation of obsolete inventory. As I said, all of the practices still apply. Many have been automated and/or digitized in progressive, larger workplaces. However, in small business land where I live and work, the simple work systems I share in this NOW *FREE* workbook can have a huge and lasting impact.
My 168-page, full color 'How to Change Work Culture' workbook and its exercises helps you and your team learn you learn how work systems shape work cultures. Their use helps blend team and organizational work cultures into one consistent, culture where kaizen is a daily work habit. Plus, I have 'personal use' experience with all of the tools I share from my past workplaces that I am happy to share.
DOWNLOAD my High Performance Work Culture Book Sample PDF
Do you want to 'stop the insanity' and eliminate the need to chase fads? If so, this workbook is for you. It contains strategies and complete exercises that give you better culture shift results in less time, and at a lower cost. Plus, you can customize my virtual or live 'How to Change Work Culture' workshop to meet the needs of any workplace.
*FREE* 'How to Change Work Culture' workbooks!
With my current update of this now-vintage, but still very value added, workbook comes the creation of obsolete inventory. As I said, all of the practices still apply. Many have been automated and/or digitized in progressive, larger workplaces. However, in small business land where I live and work, the simple work systems I share in this NOW *FREE* workbook can have a huge and lasting impact.
* If you would like one or more *FREE* 'How to Change a Work Culture' workbooks, you must pre-pay the invoiced shipping and handling costs. For the two-book minimum, this cost is $10 per book.
If you want two or more of these workbooks, please follow this link or email me at kevin@greatsystems.com. Please provide (1) your shipping location and (2) the number of books you want to buy. We can work further arrangements out from there. Cheers, and keep improving!
Three Virtual Courses are NOW Available on the Great Systems YouTube Channel
Additional downloads are a part of the different courses I offer at my Kaizen Learning Universe. In the near future, download options will include PDF, mp3, and mp4 content that supports each of the six different 'Teach Your Teams' (TYT) continuous improvement workbooks. You can learn more about the workbooks and process on that resource page.
DOWNLOAD my Lean Tools Basics and Use On-Demand Workshop Outline
DOWNLOAD my Pursuing Process Excellence On-Demand Workshop Outline
DOWNLOAD my Facilitating and Leading Teams On-Demand Workshop Outline
Videos for the first three courses are available on the Great Systems YouTube channel. The first course focuses on how to make lean tool use a daily work habit. My second course teaches leaders how to effectively pursue operational excellence. My third course looks at best practices for facilitating and leading teams.
I plan to make additional 'Teach Your Teams' downloads available as 2025 progresses.
DOWNLOAD my Lean Tools Basics and Use On-Demand Workshop Outline
DOWNLOAD my Pursuing Process Excellence On-Demand Workshop Outline
DOWNLOAD my Facilitating and Leading Teams On-Demand Workshop Outline
Videos for the first three courses are available on the Great Systems YouTube channel. The first course focuses on how to make lean tool use a daily work habit. My second course teaches leaders how to effectively pursue operational excellence. My third course looks at best practices for facilitating and leading teams.
I plan to make additional 'Teach Your Teams' downloads available as 2025 progresses.
More Great Systems Daily Kaizen Workshops
Here are some of the more popular workshops I currently offer in addition to those listed above. These workshops are available for virtual or in-person faciliation.
DOWNLOAD my 'Corrective Action Tactics and Mistake Proofing Workshop' Overview PDF
DOWNLOAD my 'How to Measure, Analyze, and Improve Next Gen Work' Workshop Overview PDF
If you would like to bring one, or both, of these workshops to your organziation, please follow this link to make your request or ask additional questions. You can also ask for more information by sending me an email at kevin@greatsystems.com. Thanks for the interest!
DOWNLOAD my 'Corrective Action Tactics and Mistake Proofing Workshop' Overview PDF
DOWNLOAD my 'How to Measure, Analyze, and Improve Next Gen Work' Workshop Overview PDF
If you would like to bring one, or both, of these workshops to your organziation, please follow this link to make your request or ask additional questions. You can also ask for more information by sending me an email at kevin@greatsystems.com. Thanks for the interest!
How to Measure and Improve Key Work Systems
CLICK on the set of improvement tips that you want to DOWNLOAD
More Continuous Improvement and OPEX Downloads
These DOWNLOADS come from popular presentations I have given over the years:
How to Implement 5S Lean Tools eBooklet PDF
The AURA of Effective Training PDF
Why Process Improvement Fixes Fail PDF
Positive Leader Feedback Drives Intrinsic Motivation eBooklet PDF
Alternatives to Discipline - Formal and Informal Recognition Options eBooklet PDF
Be Proactive with Daily Work Process Improvement eBook PDF
Empowerment Engagement and Creativity Drive Innovation PDF
How to Use the Baldrige Award Criteria to Measure Operational Excellence PDF
How to Implement 5S Lean Tools eBooklet PDF
The AURA of Effective Training PDF
Why Process Improvement Fixes Fail PDF
Positive Leader Feedback Drives Intrinsic Motivation eBooklet PDF
Alternatives to Discipline - Formal and Informal Recognition Options eBooklet PDF
Be Proactive with Daily Work Process Improvement eBook PDF
Empowerment Engagement and Creativity Drive Innovation PDF
How to Use the Baldrige Award Criteria to Measure Operational Excellence PDF