Earn a Personal Kaizen Operational Excellence Certificate
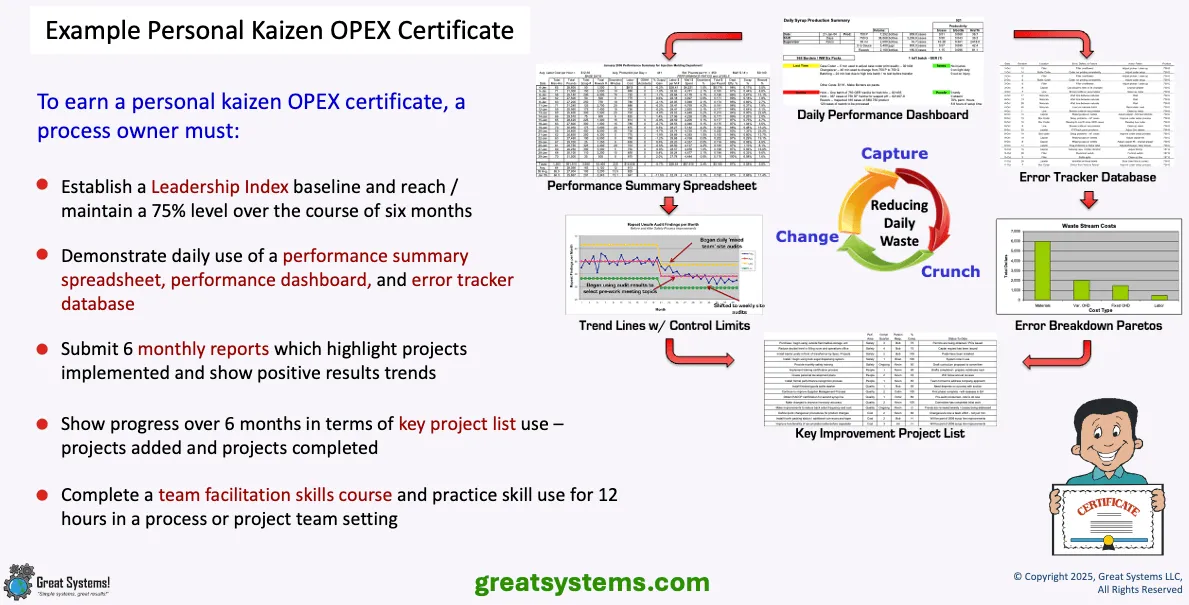
Should Process Improvement Be Optional for Leaders?
It is not uncommon to see today's organizations only engage 10-15% of their workforce in the pursuit of operational excellence. In other words, if you are not on a kaizen, lean six sigma, or operational excellence team, you are not required to improve the processes you own.
However, this results in a slow improvement rate. My Personal Kaizen Operational Excellence Certificate Process helps you save money, reduce waste, and accelerate improvement rates. More importantly, it helps you sustain your improvement initiatives.
The high performers know this. My learnings come through my own personal experiences with operational excellence successes and failures, and as an Examiner for the Malcolm Baldrige National Quality Award. Do you allow process improvement to be optional for some of formal leaders. If so, your pursuit of operational excellence will be slow and painful.
The design of my 'Personal Kaizen Operational Excellence ®' certificate approach helps you take away this option. In doing so, you will significantly accelerate your organization's progress towards levels of operational excellence.
Why is it tough to sustain a process improvement initiative?
Some organizations rely on a few process improvement teams to achieve levels of process excellence. Unfortunately, the use of that strategy will take you a while to get there.
Typically, most sites end up with only a few pockets of 'tough to sustain' excellence. Plus, your success is still dependent on the team leadership skills of your people. Al too often, front line leaders lack such skills.
The biggest problem is that this approach basically tells people "If you are not on a team, you don't have to learn and use process improvement tools."
One of the key things that hold back process improvement initiatives is the fact that in most organizations, only a small percentage of their leaders can actually use process improvement tools. We are not taught how to use these tools in our formal education. Plus, most people never get enough ‘practice reps’ using the tools with the benefit of feedback from an experienced coach.
Typically, most sites end up with only a few pockets of 'tough to sustain' excellence. Plus, your success is still dependent on the team leadership skills of your people. Al too often, front line leaders lack such skills.
The biggest problem is that this approach basically tells people "If you are not on a team, you don't have to learn and use process improvement tools."
One of the key things that hold back process improvement initiatives is the fact that in most organizations, only a small percentage of their leaders can actually use process improvement tools. We are not taught how to use these tools in our formal education. Plus, most people never get enough ‘practice reps’ using the tools with the benefit of feedback from an experienced coach.
You may have noticed that I have made many references to ‘your responsibility’ and ‘your processes’ in this training. I believe that leadership, be it at the supervisory, managerial, or director level, is a privilege. As leaders, we have more control over how we spend our time each day.
WATCH over 50 kaizen and workplace health improvement videos on my Great Systems YouTube channel.
WATCH over 50 kaizen and workplace health improvement videos on my Great Systems YouTube channel.
How do you engage all leaders in the daily pursuit of operational excellence?
It is often the case that work team supervisors, middle managers, and even those at the top actually act in a way that run counter to the efforts of the process improvement teams. In some cases, these people even restrict team performance by making it difficult for their people to go to team meetings, failing to help teams collect process analysis data, or making decisions that limit team resources. In short, they don't practice personal kaizen very well.
Most organizations see their operational excellence, lean six sigma, or process improvement teams as an add on - as a program. They fail to realize that in order to become a high performer and sustain your success, you have to do two things. First, you must consistently engage a high percentage of your people.
Second, you need to require every work team leader and process owner to practice personal kaizen. In other words, use process improvement tools on essentially a daily basis. Doing so is the optimum way to take the waste out, and increase the value, of the processes they are responsible for.
Most organizations see their operational excellence, lean six sigma, or process improvement teams as an add on - as a program. They fail to realize that in order to become a high performer and sustain your success, you have to do two things. First, you must consistently engage a high percentage of your people.
Second, you need to require every work team leader and process owner to practice personal kaizen. In other words, use process improvement tools on essentially a daily basis. Doing so is the optimum way to take the waste out, and increase the value, of the processes they are responsible for.
Why did I create the 'Personal Kaizen Operational Excellence®' certificate?
I created the 'Personal Kaizen Operational Excellence®' certificate approach for two reasons. First, I wanted to share a process with others that had worked for me as a plant manager. Second, I have grown weary of watching people chase fads. I was tired of hearing the frustrations of those who have tried to put improvement systems in place and struggled to sustain them.
From my own 40-plus years of work, I know you can do great things with improvement teams. Plus, I know that if you want to 'go faster', you have to build operational excellence skills and expectations into every employee's job.
In particular, all formal leaders must see all work as a process. All formal leaders should not only know how to use process improvement tools, but be able to tell stories of effective tool use. Ideally, they consistently practice personal kaizen daily, at least on the job.
In particular, all formal leaders must see all work as a process. All formal leaders should not only know how to use process improvement tools, but be able to tell stories of effective tool use. Ideally, they consistently practice personal kaizen daily, at least on the job.
How does one earn the 'Personal Kaizen Operational Excellence®' certificate?
This process is made up of three components - virtual workshops, virtual coaching, and most importantly, skill demonstration. First, a participant views the introductory video content and completes the pre-work assessment. Then, I virtually work with certificate participants to help them improve the processes they already own, over a 90-day period.
After three months of work, we meet again for a one-day virtual or onsite check-up. Also, we use this time to identify and meet additional training needs. At the end of six months, we gather together for one day to wrap-up the effort and celebrate our successes.
DOWNLOAD my Personal Kaizen Operational Excellence Certificate Process eBook
This process requires each participant to (1) capture key process count and ratio measures and (2) capture key process waste on a daily basis. Also, each participant (3) demonstrates monthly progress on key process improvement projects and (4) reports on their success every month.
The daily capture of key process information helps a work team leader become much more aware of their problem sources. Through the use of data collection, versus to opinion, they analyze the true root causes of their problems. Plus, they identify where the leverage points for step-change improvement exist.
The monthly reporting requirements both increase personal accountability and help each participant develop effective process improvement habits. This approach does not simply send someone to a class and ask them to change. Instead, this certificate process actually requires them to demonstrate the effects of the changes they make over a six-month time frame.
After three months of work, we meet again for a one-day virtual or onsite check-up. Also, we use this time to identify and meet additional training needs. At the end of six months, we gather together for one day to wrap-up the effort and celebrate our successes.
DOWNLOAD my Personal Kaizen Operational Excellence Certificate Process eBook
This process requires each participant to (1) capture key process count and ratio measures and (2) capture key process waste on a daily basis. Also, each participant (3) demonstrates monthly progress on key process improvement projects and (4) reports on their success every month.
The daily capture of key process information helps a work team leader become much more aware of their problem sources. Through the use of data collection, versus to opinion, they analyze the true root causes of their problems. Plus, they identify where the leverage points for step-change improvement exist.
The monthly reporting requirements both increase personal accountability and help each participant develop effective process improvement habits. This approach does not simply send someone to a class and ask them to change. Instead, this certificate process actually requires them to demonstrate the effects of the changes they make over a six-month time frame.
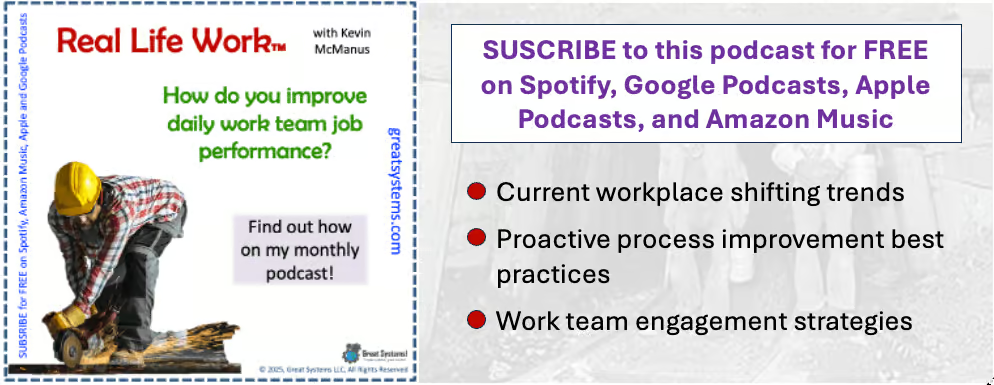
Use the player to LISTEN to my 'How to Measure Leadership Effectiveness' Real Life Work podcast
How can this certificate process significantly reduce management system waste?
I sincerely believe that if you use this certificate process in your organization, you will recover the certificate process costs BEFORE the end of the six-month certificate process itself. Why is this possible?
If for no other reason, you will significantly reduce the amount of time you spend in meetings. Also, you will improve the effectiveness of those meetings. Meetings are a process. Process improvement tools can, and have, been used to reduce meeting waste.
Additionally, the certificate process brings to light much of the key process waste that most people simply accept as a part of the job. Once the waste becomes much more obvious, the systematic causes of that waste become much more evident. You can then better identify and make the system changes necessary to reduce that waste.
If for no other reason, you will significantly reduce the amount of time you spend in meetings. Also, you will improve the effectiveness of those meetings. Meetings are a process. Process improvement tools can, and have, been used to reduce meeting waste.
Additionally, the certificate process brings to light much of the key process waste that most people simply accept as a part of the job. Once the waste becomes much more obvious, the systematic causes of that waste become much more evident. You can then better identify and make the system changes necessary to reduce that waste.
What percent of your current work processes do you consistently improve over time?
Ironically, this process pays for itself simply because such a high percentage of work team leaders don't use these tools AT ALL. That means there's a high likelihood that many of the processes they own contain costly waste. Many organizations do a great job with front line process waste reduction. However, to what degree can they demonstrate the same success with their own jobs?
As a plant manager, I expected each of my work team leaders to provide a 1-2 page summary report each month. This report contains a key project list for their processes. Plus, it includes a monthly summary of their key accomplishments and challenges. An attached performance summary spreadsheet shows DAILY process inputs and outputs in both count and ratio forms.
It is an expectation that each work team leader spends 30-60 minutes a day on these items. Spreadsheets offer a good means to organize and analyze this content. Others can review performance and progress at any time via a view of the spreadsheet itself. Typically, process owners post results trends and other charts in their process areas and on an intranet web page.
As a plant manager, I expected each of my work team leaders to provide a 1-2 page summary report each month. This report contains a key project list for their processes. Plus, it includes a monthly summary of their key accomplishments and challenges. An attached performance summary spreadsheet shows DAILY process inputs and outputs in both count and ratio forms.
It is an expectation that each work team leader spends 30-60 minutes a day on these items. Spreadsheets offer a good means to organize and analyze this content. Others can review performance and progress at any time via a view of the spreadsheet itself. Typically, process owners post results trends and other charts in their process areas and on an intranet web page.
What pecentage of your leaders make kaizen a daily work habit?
Think about it. What types of actions do your managers, work team leaders, directors, vice presidents, and owners personally take to reduce the waste that exists in their own jobs?
Am I off base here? Is it possible that these people are rarely wasteful? The hundreds of people I currently work with don't seem to think so. They know there is waste out there in the management world. These leaders know how the use of process improvement tools can minimize management system waste.
DOWNLOAD my Personal Kaizen Operational Excellence Certificate Process eBook
Am I off base here? Is it possible that these people are rarely wasteful? The hundreds of people I currently work with don't seem to think so. They know there is waste out there in the management world. These leaders know how the use of process improvement tools can minimize management system waste.
DOWNLOAD my Personal Kaizen Operational Excellence Certificate Process eBook