How to Measure and Improve Work Team Effectiveness
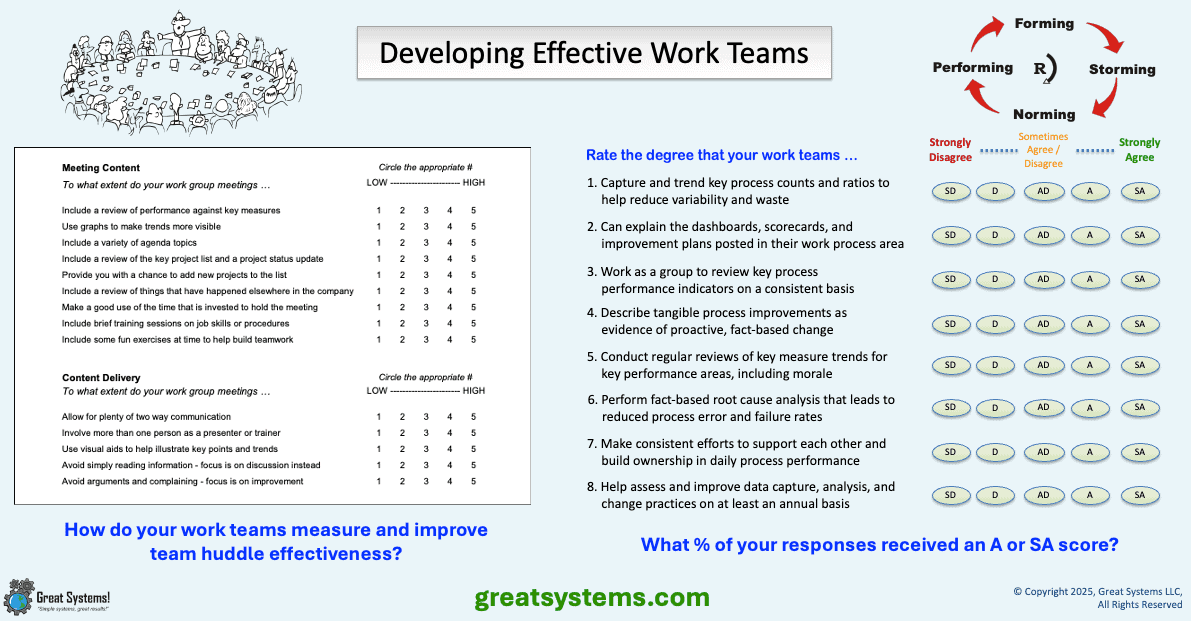
How Do You Measure and Improve Work Team Effectiveness?
Work system design determines how we spend time each day at work. The design of our work team infrastructure should drive daily kaizen, process improvement, and operational excellence, but does it? If we want to measure and improve work team effectiveness, we must first define this infrastructure.
How well defined is your work team infrastructure?
First, most work teams spend most of their work time either in, or in support of, the different value streams. Two subtypes of PROCESS work teams exist to support customer and stakeholder expectations.
Typically, very few PROCESS work teams focus on reactive problem analysis. If time allows, these work teams may invest time in proactive process and team cohesiveness improvement.
Second, two types of IMPROVEMENT work teams exist to support strategy and continuous improvement. Examples include focus groups such as safety committees, recognition teams, project teams, and leadership teams. Engineering and R&D teams spend 100% of their work time in improvement teams.
However, we can only support so many improvement teams. Value stream flow and support come first. All too often, value stream time requirements limit how much time we have left for improvement process execution.
How well defined is your work team infrastructure?
First, most work teams spend most of their work time either in, or in support of, the different value streams. Two subtypes of PROCESS work teams exist to support customer and stakeholder expectations.
Typically, very few PROCESS work teams focus on reactive problem analysis. If time allows, these work teams may invest time in proactive process and team cohesiveness improvement.
Second, two types of IMPROVEMENT work teams exist to support strategy and continuous improvement. Examples include focus groups such as safety committees, recognition teams, project teams, and leadership teams. Engineering and R&D teams spend 100% of their work time in improvement teams.
However, we can only support so many improvement teams. Value stream flow and support come first. All too often, value stream time requirements limit how much time we have left for improvement process execution.
Find Your Value Streams to Find Your Core Work Teams
All organizations have at least one value stream, as their mission is to provide a product or service. The typical value stream is made up of at least three work processes. However, in a sole proprietor small business, one person executes all such processes.
First, process inputs must be collected from suppliers, such as materials or information. Then, the value stream converts those inputs into a product or service. Finally, this process output is delivered to the customer.
In turn, at least three PROCESS work teams work to provide that good or service. It is here where we spend the bulk of our work time each day. In most workplaces, little formal time is set aside for improvement.
Keep in mind each 'team' could be as small as 1-2 people, with the same 1-2 people serving on each team. Define your value streams first. Then, define the processes that make up each value stream.
Typically, hourly staff spend 90% or more of their work time on this type of process work team. 'Working' supervisors also spend a significant portion of the work time in this way. However, it is more effective to shift formal leader time investments towards improvement when possible.
First, process inputs must be collected from suppliers, such as materials or information. Then, the value stream converts those inputs into a product or service. Finally, this process output is delivered to the customer.
In turn, at least three PROCESS work teams work to provide that good or service. It is here where we spend the bulk of our work time each day. In most workplaces, little formal time is set aside for improvement.
Keep in mind each 'team' could be as small as 1-2 people, with the same 1-2 people serving on each team. Define your value streams first. Then, define the processes that make up each value stream.
Typically, hourly staff spend 90% or more of their work time on this type of process work team. 'Working' supervisors also spend a significant portion of the work time in this way. However, it is more effective to shift formal leader time investments towards improvement when possible.
In most workplaces, we waste too much time in ineffective meetings each day! This unfortunate reality applies to all three team types as well, not just to project teams. How many of the teams in your company have effectiveness measures? How many of these teams can prove that they are improving their effectiveness over time?
WATCH over 50 kaizen and workplace health improvement videos on my Great Systems YouTube channel.
WATCH over 50 kaizen and workplace health improvement videos on my Great Systems YouTube channel.
What is a Work Team?
To begin with, what is a work team? How many different types of work teams do you have on the job
You probably have at least one work team in place (unless you are a one-person organization). These people the bulk of their work time together.
Two Subtypes of PROCESS Work Teams
In most cases, organizations have at least two of the three main types of work groups in place. Value stream work teams support external customers with their daily work. Value stream support work teams, such as Human Resources, IT, Marketing, Sales, and Accounting, support one or more value streams.
Two Subtypes of IMPROVEMENT Work Teams
Improvement work teams make up the second work team type. Multiple types of improvement teams exist, with some being temporary. Examples include leadership teams, safety committees, project teams, research and development groups, and engineering teams. At least, that is how it should work.
Larger organizations use formal improvement teams to manage and improve performance. Two such team types are common - FOCUS work teams (committees and other cross-functional groups) and PROJECT work teams.
You probably have at least one work team in place (unless you are a one-person organization). These people the bulk of their work time together.
Two Subtypes of PROCESS Work Teams
In most cases, organizations have at least two of the three main types of work groups in place. Value stream work teams support external customers with their daily work. Value stream support work teams, such as Human Resources, IT, Marketing, Sales, and Accounting, support one or more value streams.
Two Subtypes of IMPROVEMENT Work Teams
Improvement work teams make up the second work team type. Multiple types of improvement teams exist, with some being temporary. Examples include leadership teams, safety committees, project teams, research and development groups, and engineering teams. At least, that is how it should work.
Larger organizations use formal improvement teams to manage and improve performance. Two such team types are common - FOCUS work teams (committees and other cross-functional groups) and PROJECT work teams.
Leadership Style Can Also Define Team Type
Each year, IndustryWeek magazine issues a Best Plants Statistical Profile. Work team use is one of the key attributes of their annual 'Best Plant' award recipients. Also, the publication provides three operational definitions for work teams.
Natural work team: A team of employees, often hourly personnel, who share a common workspace and have responsibility for a particular process or process segment. Their direction to work is similar from an outcome perspective.
Empowered natural work teams: These work teams share a common workspace and/or responsibility for a particular process or process segment. Typically, such teams have clearly defined goals and objectives that relate to day-to-day production activities. Empowered activities might include quality assurance and meeting production schedules. Plus, work teams may have authority to plan and implement process improvements. Unlike self-directed teams, empowered work teams typically do not assume traditional "supervisory" roles and provide direction to work.
Self-directed natural work teams: These autonomous teams consist of employees who perform activities previously reserved for supervision. These work teams share a common workspace and/or responsibility for a particular process or process segment. Typically, such teams have authority for day-to-day production activities and many supervisory responsibilities.
Such responsibilities might include job assignment, production scheduling, and equipment maintenance. Other activities might include materials acquisition, training, quality assurance, performance review, and customer service. These groups are synonymous with "self-managed" work teams. All self-directed work teams are empowered.
Natural work team: A team of employees, often hourly personnel, who share a common workspace and have responsibility for a particular process or process segment. Their direction to work is similar from an outcome perspective.
Empowered natural work teams: These work teams share a common workspace and/or responsibility for a particular process or process segment. Typically, such teams have clearly defined goals and objectives that relate to day-to-day production activities. Empowered activities might include quality assurance and meeting production schedules. Plus, work teams may have authority to plan and implement process improvements. Unlike self-directed teams, empowered work teams typically do not assume traditional "supervisory" roles and provide direction to work.
Self-directed natural work teams: These autonomous teams consist of employees who perform activities previously reserved for supervision. These work teams share a common workspace and/or responsibility for a particular process or process segment. Typically, such teams have authority for day-to-day production activities and many supervisory responsibilities.
Such responsibilities might include job assignment, production scheduling, and equipment maintenance. Other activities might include materials acquisition, training, quality assurance, performance review, and customer service. These groups are synonymous with "self-managed" work teams. All self-directed work teams are empowered.
How Effective are Your IMPROVEMENT Work Teams?
However, many existing IMPROVEMENT work teams may not be very effective. For example, people may work in a team, but they may have low levels of team cohesiveness. In turn, you may be hesitant to call them teams.
Typically, close to 100% of salaried staff work time is spent one or more improvement teams of some type. However, in a small workplace, the small number of salaried staff belong to all three types of work teams.
High performance companies allocate a higher percentage of hourly staff time to 'away from work' activities for improvement team support. If this time is put to effective use, such investments will accelerate a site's process improvement rate.
Plus, improvement team engagement success drives the adoption of similar work practices in the daily work area. In many larger workplaces, such work teams exist.
Nonetheless, these people work together, and depend on each other, to get the work done each day. How people spend their time at work helps me decide when I should assign the 'team' label to a group of people.
Does your staff depend on each other to get the job done each day?
Does your work team infrastructure drive daily kaizen and operational excellence?
Typically, close to 100% of salaried staff work time is spent one or more improvement teams of some type. However, in a small workplace, the small number of salaried staff belong to all three types of work teams.
High performance companies allocate a higher percentage of hourly staff time to 'away from work' activities for improvement team support. If this time is put to effective use, such investments will accelerate a site's process improvement rate.
Plus, improvement team engagement success drives the adoption of similar work practices in the daily work area. In many larger workplaces, such work teams exist.
Nonetheless, these people work together, and depend on each other, to get the work done each day. How people spend their time at work helps me decide when I should assign the 'team' label to a group of people.
Does your staff depend on each other to get the job done each day?
Does your work team infrastructure drive daily kaizen and operational excellence?
Work Team Design Drives Daily Kaizen and Operational Excellence
How leaders define work team responsibilities affects the effective span of control ratio (people per supervisor). Span of control is a key operational parameter that leaders must optimize.
All too often, the job design requires a leader to devote too much time to personnel problem resolution instead of process improvement. In turn, leaders unintentionally constrain the rate of organizational improvement.
Plus, if excessive turnover rates exist, we only magnify this 'lack of time for improvement' problem. How much time do you design into the jobs of EACH staff member? Collectively, how much time each day do you set aside for change support, personnel development, and workforce engagement?
How Much Work Time Do You Budget for Kaizen Each Day?
Most organizations waste time each day that could be spent on process and work systems improvement. Work team job design determines a location's rate of change. It is simple math, really. If only a few jobs include time for improvement work, the rate of change will be slow.
Best practice is to budget 10% of each staff member's weekly time for formal kaizen (continuous improvement) efforts. This amounts to 4 hours per week in a 40-hour week.
Examples of formal kaizen time investment include daily huddles, monthly refresher training, and giving project feedback via social media. Ideally, teams use a portion of this time for formal waste reduction efforts.
All too often, the job design requires a leader to devote too much time to personnel problem resolution instead of process improvement. In turn, leaders unintentionally constrain the rate of organizational improvement.
Plus, if excessive turnover rates exist, we only magnify this 'lack of time for improvement' problem. How much time do you design into the jobs of EACH staff member? Collectively, how much time each day do you set aside for change support, personnel development, and workforce engagement?
How Much Work Time Do You Budget for Kaizen Each Day?
Most organizations waste time each day that could be spent on process and work systems improvement. Work team job design determines a location's rate of change. It is simple math, really. If only a few jobs include time for improvement work, the rate of change will be slow.
Best practice is to budget 10% of each staff member's weekly time for formal kaizen (continuous improvement) efforts. This amounts to 4 hours per week in a 40-hour week.
Examples of formal kaizen time investment include daily huddles, monthly refresher training, and giving project feedback via social media. Ideally, teams use a portion of this time for formal waste reduction efforts.
How Many Work Teams Do You Have?
The number of work teams you have, let alone create, matters. For example, you only have so many people with leadership skills. This limits the number of effective teams you can maintain.
How you use your work team time matters. Primarily, the value streams must take care of their customers.
Additionally, you need to know your 'total work teams' number to define team support hours, training and development expenses, and capital / major expense project needs.
These days, most medium and large-sized organizations have too many improvement teams. Many meet regularly, but they are informal. Plus, they often vary in cohesiveness levels.
Often, improvement work team missions fail to align well with strategy. Plus, they may still fail to engage key internal and external stakeholders.
A large percentage of the team time we do invest goes to non-value added topics, tangents, and discussions.
How you use your work team time matters. Primarily, the value streams must take care of their customers.
Additionally, you need to know your 'total work teams' number to define team support hours, training and development expenses, and capital / major expense project needs.
These days, most medium and large-sized organizations have too many improvement teams. Many meet regularly, but they are informal. Plus, they often vary in cohesiveness levels.
Often, improvement work team missions fail to align well with strategy. Plus, they may still fail to engage key internal and external stakeholders.
A large percentage of the team time we do invest goes to non-value added topics, tangents, and discussions.
Aren’t There More than Two Main Types of Teams?
In my opinion, no. Of course, it depends on how you answer the 'What is a team?' question. I base my team and job design definitions on (1) how work time is spent daily and (2) the need for people to work together.
Experience teaches me that any organization needs three types of work groups to reach optimum effectiveness. To effectively sustain daily kaizen and pursue operational excellence, you need effective value stream, value stream support, and improvement work teams.
Value Stream and Value Stream Support PROCESS Work Teams
These work teams consist of people who work together in the value stream or in support of it. The degree of work team self-direction, or autonomy, varies. People who work in these two types of work teams spend most of their work time with the team.
FULL TIME IMPROVEMENT WORK TEAM Full time improvement work teams include Engineering, Research and Development, and groups. These people spend 100% of their time type in the improvement team realm. Typically, their work is not seen as a process. In turn, work team effectiveness is not measured outside of department performance.
PROJECT IMPROVEMENT WORK TEAM
Quality circles, kaizen teams, tiger teams, six sigma teams, and problem-solving groups are all examples of project work teams. These groups take time away from their 'regular jobs' to develop and implement improvement projects.
For these groups, working in a team is an 'away from the normal workplace' activity. This team type is rarely found in legacy workplaces. In turn, the status quo rules.
FOCUSED IMPROVEMENT WORK TEAM
This type of improvement work team is analogous to a safety committee, steering committee, recognition board, or management group. Like project teams, they tend to be cross-functional.
Also, 'focused improvement' work teams endure over time to support the primary goals of the organization. Unfortunately, too many companies fail to measure such work team costs or effectiveness, even though significant monies are spent on this team type.
Experience teaches me that any organization needs three types of work groups to reach optimum effectiveness. To effectively sustain daily kaizen and pursue operational excellence, you need effective value stream, value stream support, and improvement work teams.
Value Stream and Value Stream Support PROCESS Work Teams
These work teams consist of people who work together in the value stream or in support of it. The degree of work team self-direction, or autonomy, varies. People who work in these two types of work teams spend most of their work time with the team.
FULL TIME IMPROVEMENT WORK TEAM Full time improvement work teams include Engineering, Research and Development, and groups. These people spend 100% of their time type in the improvement team realm. Typically, their work is not seen as a process. In turn, work team effectiveness is not measured outside of department performance.
PROJECT IMPROVEMENT WORK TEAM
Quality circles, kaizen teams, tiger teams, six sigma teams, and problem-solving groups are all examples of project work teams. These groups take time away from their 'regular jobs' to develop and implement improvement projects.
For these groups, working in a team is an 'away from the normal workplace' activity. This team type is rarely found in legacy workplaces. In turn, the status quo rules.
FOCUSED IMPROVEMENT WORK TEAM
This type of improvement work team is analogous to a safety committee, steering committee, recognition board, or management group. Like project teams, they tend to be cross-functional.
Also, 'focused improvement' work teams endure over time to support the primary goals of the organization. Unfortunately, too many companies fail to measure such work team costs or effectiveness, even though significant monies are spent on this team type.
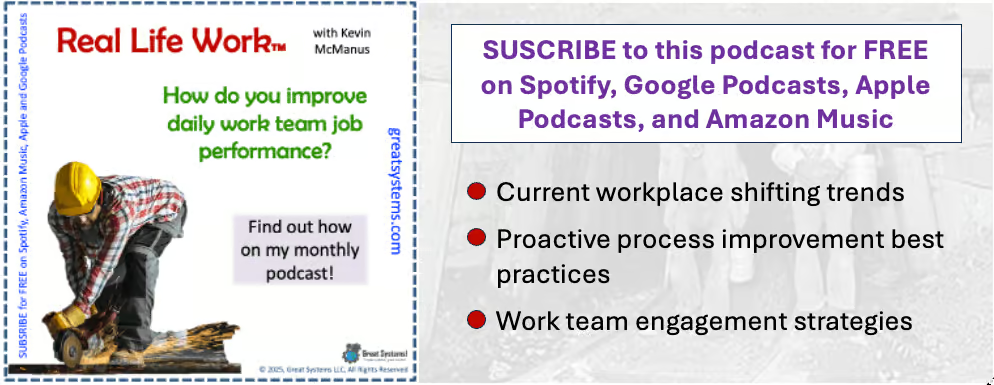
LISTEN NOW to my 'Too Many Teams, Too Little Team Effectiveness' Real Life Work podcast
How Does Team Infrastructure Drive Daily Kaizen and Operational Excellence?
If you want your work team infrastructure to drive kaizen and operational excellence, you need three types of teams in place. All staff are members of at least one process work team.
Process work teams exist in value streams or support value streams. The bulk of daily work time is spent here.
Also, people may serve roles on improvement teams. Typically, multiple types of improvement teams exist in a workplace. Examples include standing (focus) teams or temporary (project) teams.
The team structure defines how many teams of each type are needed to support strategy. In general, value stream and value stream support staff spend 90% of their time in their process work team. Engineers may spend 100% of their work time on one or more improvement teams.
Organizations need effective value stream and stream support work teams to drive continuous improvement in an organization. Since they do not have much time away from the job to meet, these work teams do not have time to develop projects.
Their role is to identify and prioritize projects that need to be implemented. The lack of project time in their jobs limits their ability to work on projects themselves.
That is why we need project improvement work teams. People need time away from their primary job to work on projects. A person may be on both a value stream work group and a project team, but that does not have to be the case.
Finally, we need 'focused improvement' work teams to maintain a constant focus on those strategic areas key to the organization. Example focus areas include safety, cost reduction, waste reduction, recognition, and management.
Process work teams exist in value streams or support value streams. The bulk of daily work time is spent here.
Also, people may serve roles on improvement teams. Typically, multiple types of improvement teams exist in a workplace. Examples include standing (focus) teams or temporary (project) teams.
The team structure defines how many teams of each type are needed to support strategy. In general, value stream and value stream support staff spend 90% of their time in their process work team. Engineers may spend 100% of their work time on one or more improvement teams.
Organizations need effective value stream and stream support work teams to drive continuous improvement in an organization. Since they do not have much time away from the job to meet, these work teams do not have time to develop projects.
Their role is to identify and prioritize projects that need to be implemented. The lack of project time in their jobs limits their ability to work on projects themselves.
That is why we need project improvement work teams. People need time away from their primary job to work on projects. A person may be on both a value stream work group and a project team, but that does not have to be the case.
Finally, we need 'focused improvement' work teams to maintain a constant focus on those strategic areas key to the organization. Example focus areas include safety, cost reduction, waste reduction, recognition, and management.
If There are Only Three Team Types, What’s with All the Different Team Names?
Cynics say that consulting firms create a lot of the different Improvement work team names to simply to make more money. For example, if quality circles don't work, why don't we call them problem solving teams?
Some group names help indicate differences in design or focus within a value stream or improvement area. For example, the structure of kaizen teams allows for faster project development (usually days) than the more traditional quality circle could produce (usually months). Shipping work teams fill that function within one or more value streams.
The degree of work team self-direction leads to additional potential work team names. Multiple strategic focus areas can result in a variety of improvement work team names.
How should we design jobs and budget resources to support improvement team involvement? How many different types of work teams do you need?
Some group names help indicate differences in design or focus within a value stream or improvement area. For example, the structure of kaizen teams allows for faster project development (usually days) than the more traditional quality circle could produce (usually months). Shipping work teams fill that function within one or more value streams.
The degree of work team self-direction leads to additional potential work team names. Multiple strategic focus areas can result in a variety of improvement work team names.
How should we design jobs and budget resources to support improvement team involvement? How many different types of work teams do you need?
Budget for Formal Team Kaizen and Operational Excellence Investments
How much cost do you formally build into your product and service cost structures to cover team support? Each team type spends its work time in different ways each day to support site's kaizen goals.
Here are some initial starting points that I have seen work well over time.
For value stream and support process work teams, an effective 5-10 minute daily huddle can have significant impact. The key is to emphasize key needs for the day, reinforce the team mission, recognize accomplishments, and update performance status. Always start here as you set aside time for formal improvement efforts.
Your site's strategic objectives should drive the number of focus teams you need. Some objectives are addressed by existing project teams or other improvement groups.
From a time investment perspective, a percentage of hourly staff typically participate on safety and recognition committees. Be careful not to form too many 'extra' teams here.
As organizations grow, their project / improvement team counts grow as well. Smaller organizations may only have one or two project teams, if that.
This is the last area to consider when you build your annual kaizen budget. As you develop a project, the use of primarily informal communication can still lead to successful project completion.
For value stream and support process work teams, an effective 5-10 minute daily huddle can have significant impact. The key is to emphasize key needs for the day, reinforce the team mission, recognize accomplishments, and update performance status. Always start here as you set aside time for formal improvement efforts.
Your site's strategic objectives should drive the number of focus teams you need. Some objectives are addressed by existing project teams or other improvement groups.
From a time investment perspective, a percentage of hourly staff typically participate on safety and recognition committees. Be careful not to form too many 'extra' teams here.
As organizations grow, their project / improvement team counts grow as well. Smaller organizations may only have one or two project teams, if that.
This is the last area to consider when you build your annual kaizen budget. As you develop a project, the use of primarily informal communication can still lead to successful project completion.
How Do You Measure Work Team Effectiveness?
Because they focus on process execution, each process work team has its own set of effectiveness factors. In my "Facilitating and Leading Teams" team effectiveness workbook, I include tools you can use to define and assess effectiveness for each team type. In general, we look at (1) results across multiple performance areas and (2) cohesiveness to measure group effectiveness.
Cohesiveness is necessary to help drive high levels of output. Keep in mind that most work groups don't fail because of low cohesiveness. Instead, teams often fail due to a lack of proper support in the areas of information, recognition, resources, and alignment.
Example process output measures usually fall into the quality, safety, cost, and growth performance areas. Cohesiveness measures include absenteeism and tardiness rates, survey score results, and retention rates.
Most process work teams use some set of scorecard measures. Primarily, project work team measures look at performance to milestones and budget. Sadly, leaders often fail to track cohesiveness for project work teams.
Similarly, leaders often fail to measure improvement work team performance. Do you measure safety committee or leadership team effectiveness?
Often, measures of focus team effectiveness come from annual survey statement responses. Improvement and project implementation rates versus team cost provide additional focus team effectiveness measures.
Cohesiveness is necessary to help drive high levels of output. Keep in mind that most work groups don't fail because of low cohesiveness. Instead, teams often fail due to a lack of proper support in the areas of information, recognition, resources, and alignment.
Example process output measures usually fall into the quality, safety, cost, and growth performance areas. Cohesiveness measures include absenteeism and tardiness rates, survey score results, and retention rates.
Most process work teams use some set of scorecard measures. Primarily, project work team measures look at performance to milestones and budget. Sadly, leaders often fail to track cohesiveness for project work teams.
Similarly, leaders often fail to measure improvement work team performance. Do you measure safety committee or leadership team effectiveness?
Often, measures of focus team effectiveness come from annual survey statement responses. Improvement and project implementation rates versus team cost provide additional focus team effectiveness measures.
How Effective Are Your PROJECT IMPROVEMENT Work Teams?
Smaller organizations may not have PROJECT work teams. Instead, leaders manage improvement projects on their own, and they engage with their teams as necessary. At least, that is how it should work.
PROJECT teams stay intact until the team finishes their project. In some cases, the team remains intact to work on a new project, as with some Quality Circle or Kaizen Team processes.
Engineering PROJECT teams are one example of a PROJECT team. However, these project teams often do not gather for every meeting. Plus, the job designs of Engineering PROJECT team members include process improvement work time (often 100%).
Limiting factors to PROJECT team effectiveness include leadership skill levels, team group dynamics skills, data availability, and work time available.
PROJECT teams stay intact until the team finishes their project. In some cases, the team remains intact to work on a new project, as with some Quality Circle or Kaizen Team processes.
Engineering PROJECT teams are one example of a PROJECT team. However, these project teams often do not gather for every meeting. Plus, the job designs of Engineering PROJECT team members include process improvement work time (often 100%).
Limiting factors to PROJECT team effectiveness include leadership skill levels, team group dynamics skills, data availability, and work time available.
How Effective are Your FOCUS IMPROVEMENT Work Teams?
All organizations have at least one IMPROVEMENT work team. In some cases, focus teams are known as cross-functional teams. Focus teams meet regularly to address key organizational focus areas.
For example, the senior leadership group is a focus team that meets on a regular basis. Committees and task forces are other examples.
Focus work teams exist to tackle a specific problem or perform a specific task. Their representation includes different functional disciplines or process segments. In some cases, focus teams form on an ad hoc basis.
Other examples of common focus work teams include safety, training, and recognition committees. Also, customer satisfaction teams, waste reduction teams, planning teams, and leadership teams may exist.
Focus work team performance is more difficult to measure. This is due to the cross-functional membership and variability in team process types. In many cases, focus team members do not even track the amount of time they invest in the one, or more, focus teams they are on.
However, significant savings and team performance gains can be made when leaders optimize their use of focus work teams and project work teams.
For example, the senior leadership group is a focus team that meets on a regular basis. Committees and task forces are other examples.
Focus work teams exist to tackle a specific problem or perform a specific task. Their representation includes different functional disciplines or process segments. In some cases, focus teams form on an ad hoc basis.
Other examples of common focus work teams include safety, training, and recognition committees. Also, customer satisfaction teams, waste reduction teams, planning teams, and leadership teams may exist.
Focus work team performance is more difficult to measure. This is due to the cross-functional membership and variability in team process types. In many cases, focus team members do not even track the amount of time they invest in the one, or more, focus teams they are on.
However, significant savings and team performance gains can be made when leaders optimize their use of focus work teams and project work teams.
How to Improve IMPROVEMENT Work Team Performance
All organizations have one, or both, of these improvement team types. However, one or two people may be the only team members in play.
PROJECT IMPROVEMENT work teams focus more on singular change efforts that are often much larger in scope and involve more external stakeholders. Examples of project work teams include process improvement teams, kaizen teams, tiger teams, quality circles, and engineering teams.
Leadership teams are the most common FOCUS IMPROVEMENT work team type. Safety committees and recognition teams are examples of common hourly workforce focus improvement teams. A Kaizen process Steering Committee is another example of a IMPROVEMENT work team.
To improve PROJECT and FOCUS IMPROVEMENT work team performance, leaders need to manage team dynamics and engagement levels. Plus, team leaders must manage the meeting and project development processes, and between-meeting activities. It is common for improvement teams to have multiple projects active at one time.
Keep in mind that with BOTH team types, different team members can act as project leads. Plus, team mix may change more often over time. Both factors make meeting and project management more of a challenge.
PROJECT IMPROVEMENT work teams focus more on singular change efforts that are often much larger in scope and involve more external stakeholders. Examples of project work teams include process improvement teams, kaizen teams, tiger teams, quality circles, and engineering teams.
Leadership teams are the most common FOCUS IMPROVEMENT work team type. Safety committees and recognition teams are examples of common hourly workforce focus improvement teams. A Kaizen process Steering Committee is another example of a IMPROVEMENT work team.
To improve PROJECT and FOCUS IMPROVEMENT work team performance, leaders need to manage team dynamics and engagement levels. Plus, team leaders must manage the meeting and project development processes, and between-meeting activities. It is common for improvement teams to have multiple projects active at one time.
Keep in mind that with BOTH team types, different team members can act as project leads. Plus, team mix may change more often over time. Both factors make meeting and project management more of a challenge.